3D printing for supercar design

3DGBIRE and Briggs Automotive Company announce Additive Manufacturing Partnership.
Source: 3dgbire.com
Challenge
Previously, BAC would outsource parts to third party vendors. BAC wanted to introduce 3D Printing into their car production process, to aid them with R&D and prototyping, to manufacturing aids, to the production of end use parts.
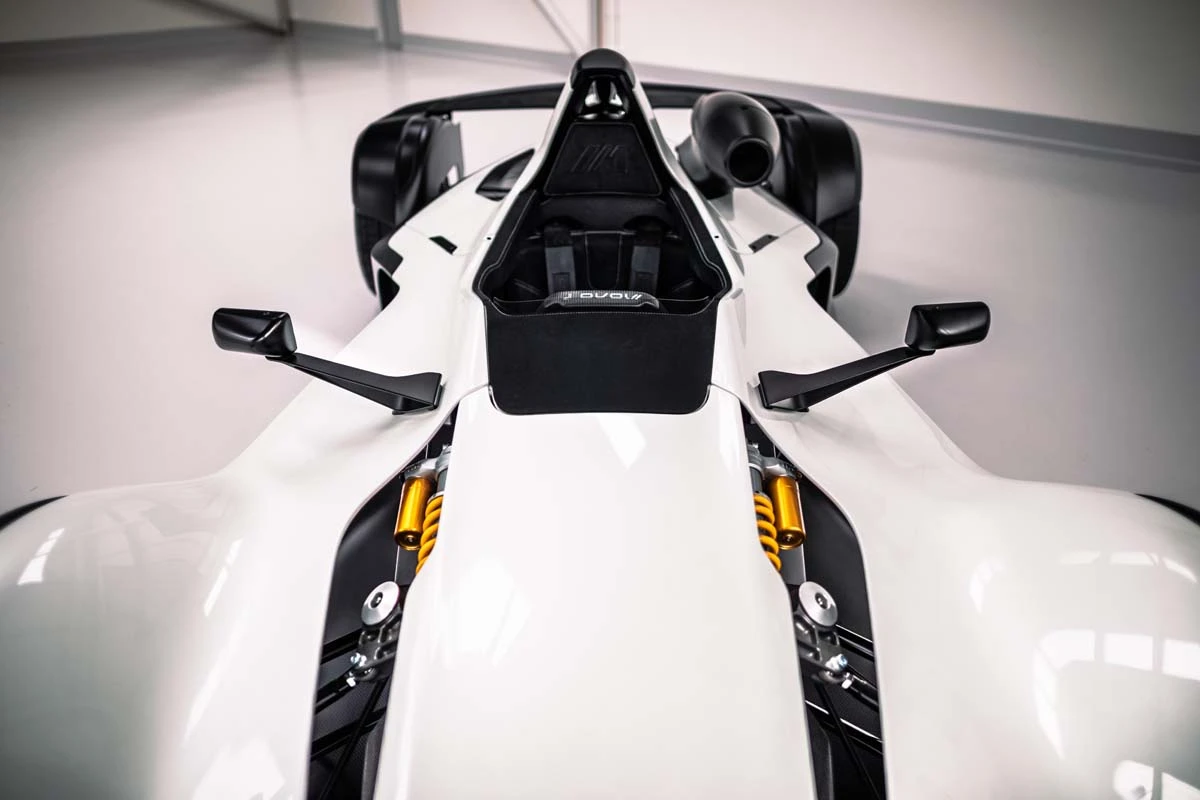
Solution
3DGBIRE and Briggs Automotive Company (BAC) have announced their partnership to enable the continued adoption of 3D Printing. BAC began their additive manufacturing journey with the launch of the Mono R – a higherperformance, lighter and more advanced new generation of the iconic Mono. Using the combined resources of Application Engineers from 3DGBIRE and Ultimaker, BAC were able to prototype and produce over 40 3D printed parts.

“This partnership is yet another development in the relationship between the automotive industry and additive manufacturing. The introduction of 3D Printing into the car production process has proven to be beneficial at numerous stages. From R&D and prototyping, to manufacturing aids, to the production of end use parts, 3D printing is saving businesses like BAC money and slashing lead times. This is just the tip of the iceberg, 3D Printing is becoming a prominent force in automotive manufacturing with companies like BAC leading the charge and developing new applications for the technology. We can’t wait to help BAC further integrate 3D Printing into their business and investigate what other doors we can open with regards to manufacturing.”
Daniel Abram, General Manager - 3DGBIRE Ltd
Results
By 3D printing parts using Ultimaker S5 FFF 3D Printers, BAC has been able to reduce the design-to-manufacture timeframes of complex geometrical components and bring production in house. The versatility of Ultimaker’s Open Source Material Alliance allowed 3DGBIRE to facilitate BAC with DSM industrial grade high-performance polymers to produce bespoke production parts for each vehicle, at a reduced cost.
“It’s been fantastic, it allows us to create something and have it ready to test in a matter of hours is game changing for BAC. We’re already using it in all aspects of production from R&D to prototyping to end use parts.”
Adam Mughal Lead 3D Designer - Briggs Automotive Company

Costs
“3D printing in-house has had a big impact on cost savings for particular parts; for example the cost price of our wing mirrors used to be £60, now we can print them in two parts for just £10 total cost. 3D Printing really has been a revelation for us at BAC.”
Adam Mughal Lead 3D Designer - Briggs Automotive Company
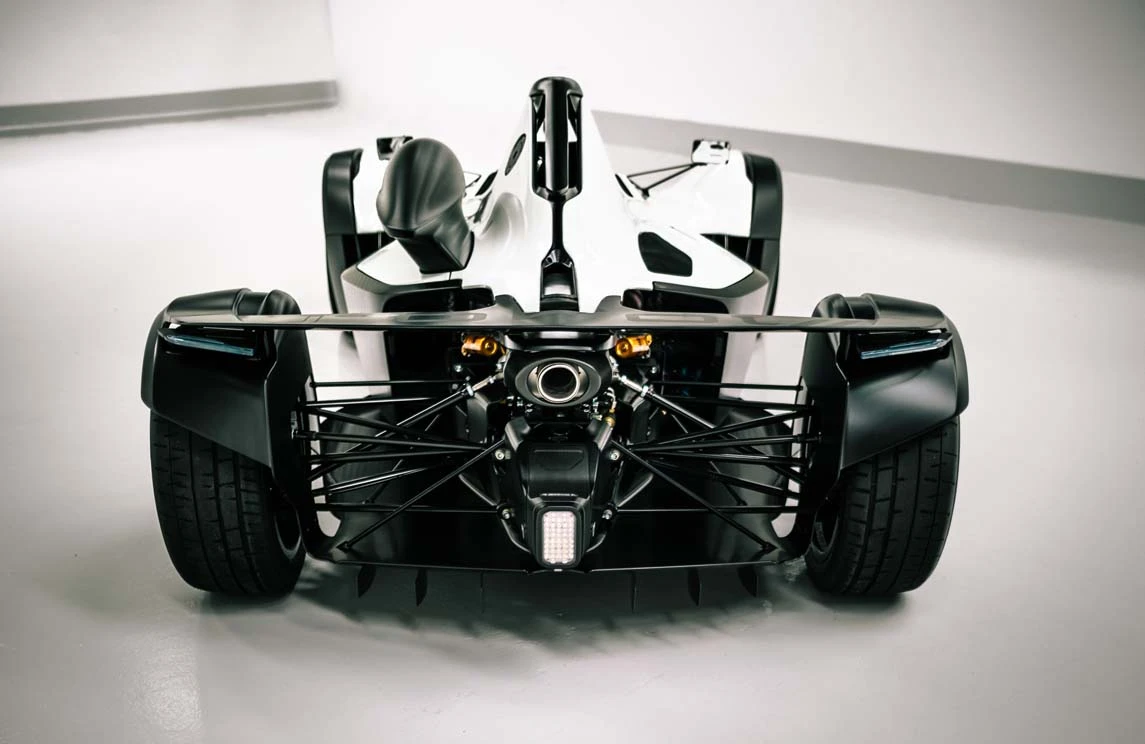
Do you want to discover other 3D printing applications in the Automotive sector?
In Same Category
- Krones: Optimized 3D-printed parts & spares for customers anywhere
- La stampa 3D nel settore farmaceutico
- Tre Zeta Group - 3D printing for the footwear sector
- Angelini Pharma: from research to production of personalized drugs thanks to 3D printing
- Nissan implements 3D printed tools, jigs and devices in its assembly lines
Related by Tags
- Krones: Optimized 3D-printed parts & spares for customers anywhere
- 3D printing for the production of sheet metal bending dies
- Bambu Lab X1E: multifilament 3D printing in industrial applications
- 3D printing for the Education and STEM disciplines: the FabLab Poliba experience
- Fireproof additive manufacturing: the benefits of flame retardant materials in modern industry
Leave your comment