3D printed tool for capping systems
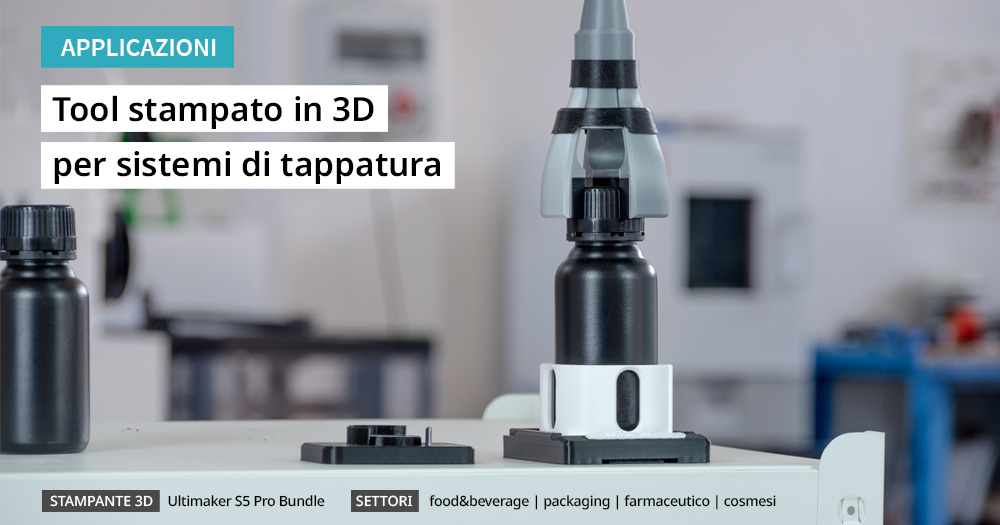
The use of 3D printing is totally revolutionizing the manufacturing industry through different applications. From the food&beverage to the packaging sector, from the cosmetics to the pharmaceutical sector, additive technologies allow to meet a constantly growing demand thanks to the development of innovative and performing tools in a very short time and at low cost.
One of the key issues in the production of food, cosmetics or drugs lies in the conservation phase, and therefore, in the packing phase too.
To preserve the integrity, the freshness or the fragrance of a product, it is fundamental that the product is properly packaged or bottled, according to the specific customer requirements.
The request coming from the Large-Scale Retail Trade or from the different distribution sectors may vary considerably during the productive stage depending on the season, on the size convenience or on the consumer purchasing power.
Reducing machine stoppage times allows to efficiently meet the needs, increasing the loyalty and satisfaction degree of customers.
Responding to the production needs of a customer, the industrial R&D department of Crea 3D started the development of a tool, an end-effector for capping in thermoplastic material adaptable on semi-automatic systems depending on the quantity to produce.
Thanks to the use of FFF 3D printers, it is possible to create a device that fits perfectly the ergonomics of the bottle so as to ensure a perfect closure, drastically reducing the number of metal parts and speeding up assembly and/or replacement operations.
The tool obtained has a weight of just 90g being composed of 99% printed parts, it is configured as a central body made with BASF Ultrafuse PRO1 filament, on which the three gripping levers can slide, which in turn contain the grippers in flexible polyurethane (TPU), necessary to guarantee an optimal closure yet not making signs of usury on the cap.
The tightness and the elasticity of the parts is guaranteed by loop locking systems in affordable flexible material.
The configuration of the capping makes it possible to replace and print the grippers depending on the diameter and on the shape of the cap, by reducing the number of the required warehouse spare parts.
Our additive manufacturing plants, and especially the Ultimaker S5 Pro Bundle, allow to realise the entire tool in just 19 hours with a total cost of the parts for less than 12€. And by doing so, it is possible to meet the original customer’s demand, which required longer delivery times of about 2-3 weeks by an external supplier and a total cost of 350€.
The Material Station, integrated in the Pro Bundle solution provided by Ultimaker, guarantees reliability in printing processes thanks to the flow sensors and to the quantity and humidity control of the material.
The system provides for the loading of a new spool in the case of insufficient filament without user intervention, making the printing process fully automated, reliable and repeatable.
During boot, the print head realises a mapping of the build plate through the active position monitoring of the build plate to stabilise the adhesion of the first layer and to avoid phenomena such as deformation and shrinking, making the printing of complex geometries possible.
The integrated webcam allows the management of the print queues through the application of Ultimaker Digital Factory, directly from the CAD workstation, avoiding machine downtime during loading/unloading operations of new spools.
During the extrusion process, the safety of the operator and working environment is ensured by the Air Manager, with its self-regulating air filtration system.
The advantage is not only economically successful, because the additive manufacturing processes allow to think about the design and produce the parts developing new shapes and materials concepts.
The consumer safety represents the main issue in these fields, and so the introduction of detectable materials allows to prevent any contamination within the production lines in the case of accidental breakage of parts.
Reduced waiting times allow to devote more attention to the product development and to testing stages.
Any change can be re-elaborated in a short time and the component can be printed in a few hours. Customer’s request turns out to be satisfied as a result of:
- short product development times
- reduced prototyping and production costs
- flexibility in production
- simplification of assembly & maintenance phases
- effectiveness guarantee of the component thanks to the most hours dedicated to the testing steps
- consumer protection and confidence thanks to resistant and detectable materials.
In Same Category
Related by Tags
- Krones: Optimized 3D-printed parts & spares for customers anywhere
- 3D printing for the production of sheet metal bending dies
- Bambu Lab X1E: multifilament 3D printing in industrial applications
- 3D printing for the Education and STEM disciplines: the FabLab Poliba experience
- 3D printing and footwear: the FuSa shoe
Leave your comment